Checking Out the Conveniences of a Chemical Defoamer in Production and Production
The combination of chemical defoamers in manufacturing and manufacturing processes provides a critical benefit by addressing one of the consistent difficulties in industrial operations: foam control. As makers aim to maximize processes and enhance client fulfillment, the function of chemical defoamers becomes progressively vital.
Value of Foam Control
While the presence of foam in manufacturing processes can sometimes appear safe, efficient foam control is critical for optimizing operational performance and product quality. Foam can disrupt numerous stages of production, resulting in ineffectiveness that might expand and boost costs processing times. In sectors such as food and beverage, pharmaceuticals, and chemicals, uncontrolled foam can obstruct equipment, disrupt automated systems, and ultimately cause product variances.

Applying effective foam control approaches not only enhances productivity but likewise supports regulative compliance in markets where foam can bring about ecological problems. By making use of chemical defoamers, makers can minimize these obstacles, guaranteeing smoother operations and higher-quality final result. Inevitably, prioritizing foam control is an essential aspect of manufacturing that can yield substantial benefits in regards to efficiency, product, and safety and security reliability.
Types of Chemical Defoamers
What types of chemical defoamers are available for making procedures, and just how do they vary in application? Chemical defoamers can be categorized right into 3 major types: silicone-based, natural, and not natural defoamers. - Chemical Defoamer

Organic defoamers, usually acquired from all-natural oils or fatty acids, are effective in an array of applications, consisting of food and drink production. They are usually liked for their lower poisoning and environmental impact, guaranteeing conformity with industry policies.
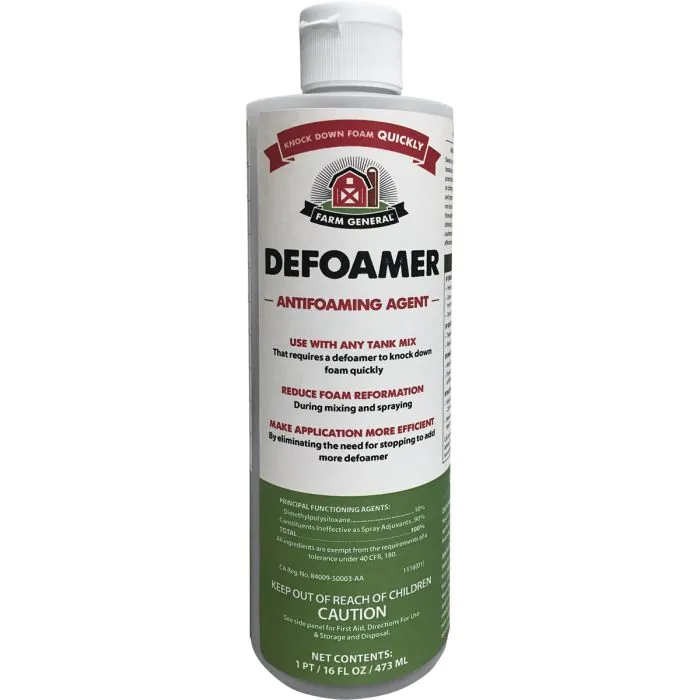
Each kind of defoamer offers distinctive purposes based on the chemical structure and the particular needs of the production procedure, permitting makers to select the most appropriate option for their specific needs.
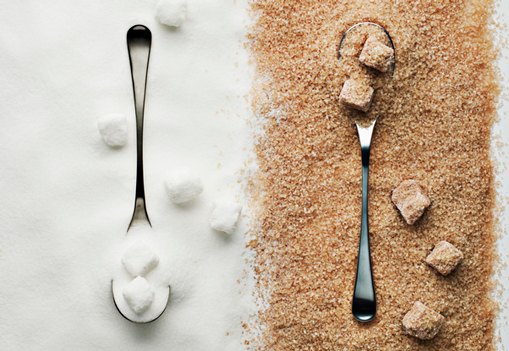
Advantages in Production Effectiveness
Chemical defoamers play an important function in boosting manufacturing efficiency by successfully managing foam generation during various procedures. Foam can hinder manufacturing rates, disrupt devices operation, and lead to costly downtime. By integrating chemical defoamers, manufacturers can alleviate these concerns, guaranteeing smoother process and raised general performance.
The use of chemical defoamers helps maximize the functional performance of tools such as activators, mixers, and pumps. With minimized foam, these devices can run at their planned ability, lessening the threat of overflow and allowing constant handling. This leads to better source application and greater throughput.
Moreover, chemical defoamers promote faster processing times by lowering the moment needed for foam elimination. This acceleration can dramatically influence manufacturing routines, allowing manufacturers to fulfill customer demand extra properly. Furthermore, the use of defoamers adds to reduce energy usage, as equipment operates a lot more successfully with minimized foam disturbance.
Influence On Product Top Quality
Foam control is not just important for preserving performance in manufacturing procedures but likewise plays a considerable duty in ensuring product quality. Excessive foam can introduce air into solutions, bring about disparities in the final product. This can manifest as defects such as voids, irregular textures, or subpar surfaces, which threaten the designated top quality and efficiency of the item.
Furthermore, foam can hinder the homogeneity of mixtures, leading to uneven distribution of energetic ingredients. In industries such as finishes, cosmetics, and food production, this can cause variations in shade, taste, and general performance. By making use of a chemical defoamer, manufacturers can mitigate these threats, making certain that items meet stringent quality specs.
In addition, managing foam can enhance the security of suspensions and solutions, which is critical for making sure shelf-life and consumer satisfaction. With improved product consistency and reduced flaws, manufacturers can attain higher standards of quality control, ultimately leading to boosted customer trust fund and brand commitment.
Cost-Effectiveness and ROI
Efficient foam control not only enhances product top quality yet likewise contributes substantially to the total cost-effectiveness of making procedures. The use of chemical defoamers minimizes foam-related problems, which can otherwise result in production hold-ups, devices breakdowns, and raised power intake. By decreasing foam, suppliers can enhance their procedures, resulting in greater throughput and efficiency.
Buying chemical defoamers can view website yield a considerable roi (ROI) The preliminary prices associated with these ingredients are typically balanced out by the financial savings recognized from reduced downtime and enhanced product yield. Improved item top quality can reduce waste and remodel expenses, better boosting economic efficiency.
Furthermore, effective foam control can lead to reduced water and energy usage, adding to reduced functional prices. This is specifically vital in industries where source performance is vital. By incorporating chemical defoamers into their procedures, producers can attain long-lasting cost savings while maintaining competitive pricing in the marketplace.
Final Thought
In conclusion, the assimilation of chemical defoamers in manufacturing and production processes is important for enhancing functional effectiveness and boosting product quality. The benefits used by chemical defoamers not just sustain regulatory conformity however likewise provide an affordable side in the manufacturing landscape.
The assimilation of chemical defoamers in production and production processes uses a strategic advantage by addressing one of the click here for info consistent difficulties in industrial operations: foam control.While the visibility of foam in making procedures can often seem harmless, reliable foam control is important for optimizing operational efficiency and item high quality.Chemical defoamers play an look here essential role in improving making performance by effectively managing foam generation during numerous procedures.Additionally, chemical defoamers facilitate faster handling times by reducing the time required for foam removal. In addition, the usage of defoamers adds to decrease energy intake, as machinery operates more efficiently with reduced foam interference.